Trade fair highlight 06. September 2023
New Manufacturing Technologies for Metallic Bipolar Plates
1 / 5

Bipolar plate production and Characterization of metal foils
2 / 5

Tool for passive high-pressure sheet forming of bipolar plates
3 / 5

Hammer manufactured by a combination of hydroforming and injection molding
4 / 5

Linked value chains and possible data spaces
5 / 5
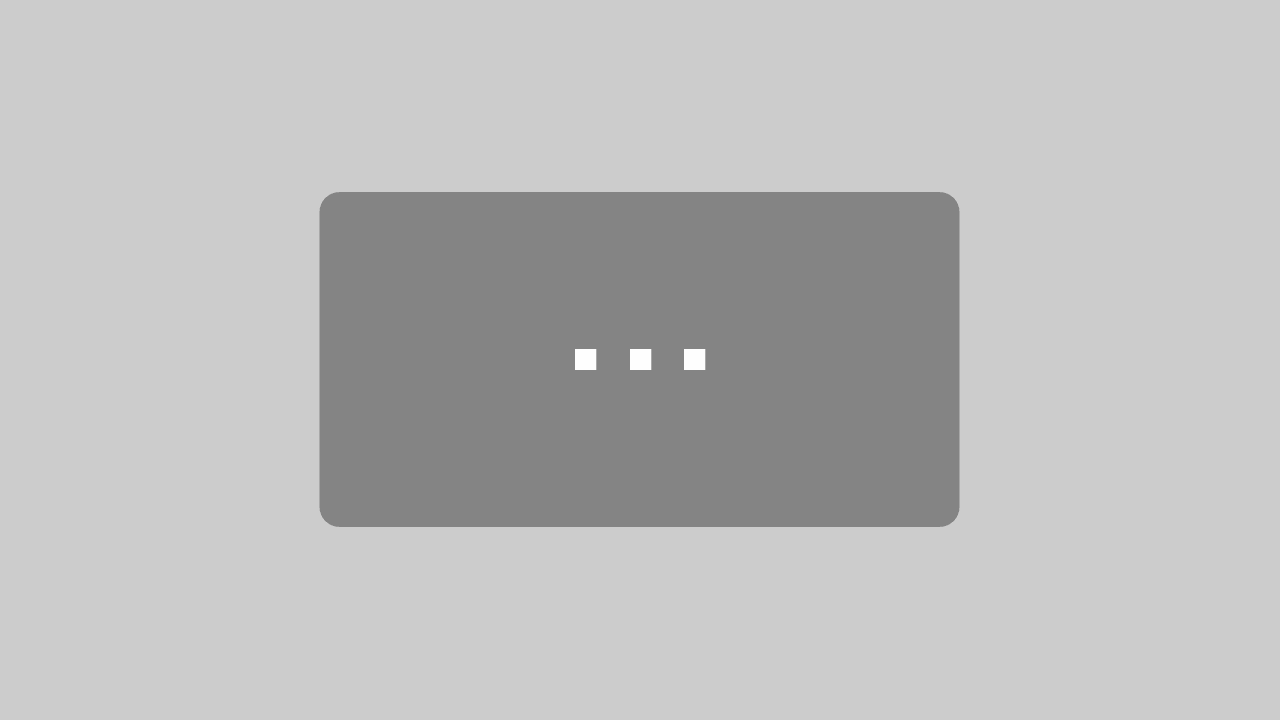
By loading the video you accept YouTube's privacy policy.
Learn more
Conventionally, bipolar plates (BPP) are produced, e.g. by deep drawing, in medium quantities at comparatively high costs. Various production processes for BPP were therefore investigated and compared at Fraunhofer IWU. Not every process is suitable for every type of BPP. Among other things, the field of application is decisive for the effectiveness of the production process. In addition to the production rate, the type of fuel cell or electrolyzer in which the BPP will later be used plays a role, i.e. whether mobile or stationary applications are involved, for example. The knowledge gained is incorporated into the technology toolbox and provides the industry with an excellent basis for finding the optimum manufacturing process in each case: From hydroforming for smaller series and prototypes to hollow embossing for medium quantities or roll embossing for the largest quantities. On the way to mass production of BPP, a first important step has already been completed: The flow field geometry of a BPP has been further developed in such a way that it can be produced using alternative processes, such as continuous roll stamping, in addition to the usual ones. Prototypes have already been realized using hydroforming, also known as high-pressure sheet forming (HBU). For this purpose, the process was further developed with the variant of passive hydroforming. In this process, the forming pressure is generated directly in the die by the ram force, which simplifies the plant technology and reduces energy consumption and cycle time. Currently, the next technological step towards mass production is being developed and BPP will be produced by continuous roll stamping. The aim is to achieve a production rate of at least 120 BPP per minute. This is about twice what industrial companies currently achieve with classic deep drawing or embossing. The efficiency of the fuel cells remains stable at a high level.